ATILIUS is an innovative fluidic subsystem for space electric propulsion designed to reduce material consumption and waste on Earth and to mitigate further debris in space. The project aimed to design, simulate, manufacture, test and validate a highly efficient solid propellant fluidic subsystem for a small satellites space propulsion system, to be manufactured through metal 3D printing (LPBF – laser powder bed fusion) by using recycled material as feedstock.
With the advent of the New Space Economy, the number of satellites orbiting the Earth is increasing abruptly, with an ever-growing risk of exacerbating the space debris issue. The best solution to mitigate this environmental threaten is to de-orbit the satellites at the end of their operative lifetime using electric propulsion systems to decrease the orbit until a safe and controlled re-entry in the atmosphere is achieved. Mass budget constraints, above all in CubeSats (i.e., satellites whose mass is <50 kg), often prevent the addition of the propellant and of the propulsion systems necessary for end-of-life manoeuvres.
REGULUS-50-I2 is an innovative low-thrust electric propulsion system developed by T4i specifically for small satellites, whose fluidic subsystem design has been optimized, thus increasing its thermal efficiency, and allowing to store enough propellant for both standard orbital manoeuvres and de-orbiting.
REGULUS-50-I2 is unique thanks to the use of solid iodine as propellant. Iodine is not toxic and allows to have a no-pressurized tank and its use reduces the overall system volume. Iodine needs to sublimate to operate. The thermal paths of the fluidic subsystem have been carefully re-designed to minimize the thermal leaks thus improving the overall thermal efficiency. A numerical tool for the thermal analysis and optimization has been developed and validated during the project. The project represents a technological challenge and has a huge market potential for the entire aerospace industry. It will contribute to find solutions to open critical points along the AM process chain, from design phase to finishing.
Moreover, ATILIUS project took the opportunity to 3D print with LPBF the device by using as raw material a “green powder”, i.e., a metal powder generated from scrap recycling (scrap from failed prints, residual powder, support structures and other materials then gas atomized), in a reduction of raw material consumption through to the second use of parts or material (including waste from manufacturing process), validated the performances of such a green approach.
Regarding the circular indicators:
CIR1 – ATILIUS has been printed by using recycled powders, e.g., powders coming from scrap, featuring a % circular inflow index > 97%.
The use of recycled powders has been proven to be feasible, and reliable. The robustness of the material has been proven by means of a vibration test performed onto the ATILIUS subsystem. The vibration test gave positive outcomes, proving that the AM products can be produced with recycled powders also in the case of demanding requirements in terms of resistance and mechanical properties.
CIR3 – The material wasted while manufacturing the ATILIUS subsystem will be reintegrated in the cycle to produce new recycled powder, in an approach perfectly in line with the circular eco
nomy concepts.
CIR5 – The reduction of the carbon footprint related to the use of recycled powders has been estimated by means of a LCA onto the ATILIUS subsystem as 25.5%.
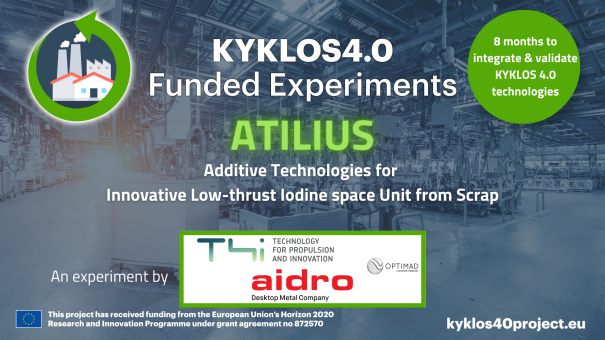