Customization (to specific needs of customers) of the solution related to optimization of maintenance service process of machine tools through process mining techniques, within the open-source KNIME ® predictive analytics platform environment. Such optimization can allow reduction of throughput time and cost of maintenance service process.
ERMES solution includes the deep-dive analysis, discovery, monitoring and improvement of as-is maintenance service processes, revealing the to-be efficiencies the business could benefits from. It takes all of the process data generated by a business process (Event log files) and mines it for insight on potential improvement, focusing on finding better, more efficient pathways in operations. The goal is to identify optimal process paths that require minimal costs, resources and time. This allows businesses to increase speed and accuracy, allowing teams to focus on doing what they do best as efficiently as possible. The solutions within ERMES will be developed for machine tools/production equipment sectors but it can be replicated in different manufacturing sectors. ERMES provides a solution pivotal in bringing about a change towards a more circular manufacturing. With its methodology the project enables a deep integration and optimization of the overall maintenance service process. This approach will also boost process re-use and renovation through extension of useful life of equipment, decreasing of waste and enabling efficient organization and execution of logistics and maintenance-related tasks.
Main features and capabilities of the ERMES consulting service:
- Support to customer for customization and implementation of requirements
- Support to customer for legacy data collection and aggregation
- Support to customers for AI-based workflow/solution for process mining implementation related to the analysis of maintenance service processes (here named the ‘business process’) . The workflow/solution includes the following capabilities:
- Discovery: identifies the business processes, maps and analyzes an organization’s existing business processes, uncovers the process steps that they are not aware of, and realizes process deviations. A discovery technique takes an event log and produces a process model without using any prior information
- Conformance check: is a technique to compare a process model of the actual process with an event log of a standard reference process (best practice) defined by the company. The goal is to check if the event log conforms to the model and vice versa and then Identifying the non-conformant tracks
- Performance check: it calculates the throughput time and cost of the maintenance service process (and eventually other relevant KPIs)
- Enhancement: The goal is to extend or improve an existing process model using information about the actual process model. Enhancement follows below steps:
- Identifying process bottlenecks (root cause analysis)
- Recommendation for improvement
- Preventive maintenance plan: provides optimal time to replace components on the basis of past events and future production plan
- Support to customers for results assessment
Regarding the circular indicators:
CIR1 – Removing bottlenecks within the maintenance service processes means to cut the use of the resources (consumables, spares, etc.) for unnecessary tasks. A 10%-15 of reduction is expected.
CIR3 – Increasing of efficiency measured through the reduction of overall energy involved in the process. In fact, each process deviations (respect to standard nominal maintenance service process) contribute to efficiency losses. By removing process deviations an increasing of 10-15% of efficiency could be achieved.
CIR4 – Increasing of 10% of life of component thanks to optimal preventive maintenance planning (due to less frequent scheduled replacement of components). This is can be measured comparing the ‘nominal’ preventive interval of machine (taken from machine operative handbook) with the new ones.
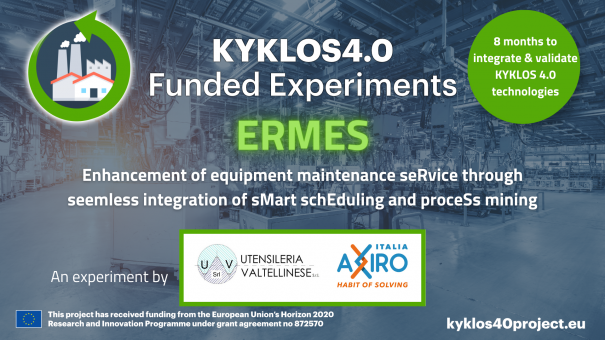