The solution, called AI-extensometer, consists of a software platform made of scripts and datasets developed onto and to be used with the MaCh3D testing device.
MaChAwAI project developed an AI-extensometer tool. AI-extensometer is a virtual extensometer platform that consists of an AI to predict the material stress-strain curve starting from the load-displacement curve of simple tensile tests performed onto the MaCh3D smart universal testing machine. Combining the ease-of-use and the compactness of the MaCh3D device together with accurate results coming from the AI extensometer makes material testing more affordable and more applicable, even possible at production floor, but as accurate as in laboratories.
Non-instrumented tensile tests, performed on any testing machine, are affected by both deterministic and random factors that introduce errors in the test results. Deterministic errors can be predicted and then excluded from test results by post processing of data traditionally made with analytical or numerical techniques that require model implementation and its characterization. On the other side, random factors are not easily detectable. Due to the specific features of the device, the MaCh3D testing procedure minimises random errors in tests, eliminating errors introduced by the operator. Counterpart of this advantage is a larger effect of deterministic errors. Artificial intelligence is identified as a novel approach to correct errors in non-instrumented tensile tests, capable of simulating a direct strain measure replacing traditional contact or non-contact instrumentations (like strain-gages, extensometer and optical measures) that introduce complexity into test procedure and require time for setup. AI can be even more precise than previous methods because it can be continuously improved while applied.
MaChAwAI project developed a so-called AI-extensometer (artificial intelligence virtual extensometer) that is capable of a precise mechanical properties evaluation, with errors from 0 to 10% depending on the specific mechanical parameter under consideration. The developed solution consists in the MaCh3D device and software (already developed) integrated with the AI-extensometer software platform (developed within the framework of the Kyklos4.0 experiment) composed of the following parts/modules:
- Server module: responsible of loading the AI model and process the tensile test data;
- The AI model: the model itself, with architecture definition and the trained weights and parameters;
- The client: the user interface to upload the test data and obtain the AI-extensometer curve;
- The data used for AI Model training and test procedures;
The use of the MaCh3D smart material testing solution together with the AI-extensometer results in an easy and quick way to perform material testing, with almost the same accuracy of complex laboratory tests, applicable directly in industrial production areas with no specific requirements for hardware installation and no particular expertise by the operator.
Regarding the circular indicators:
CIR2 – Simplified material testing (Smart Material Testing) allows a wider number of tests and a wider application for quality control of materials. This impact positively in the adoption of recycled materials because of punctual tests will give immediate feedback on material performances and reliability.
CIR3 – Smart Material Testing allows to improve the efficiency of those manufacturing processes in which energy consumption is directly related to material performances (i.e. Additive Manufacturing, INjection moulding, …). Energy consumption can be then optimised according to the final material properties to be obtained during the process.
CIR4 – Smart Material Testing allows to detect production failures directly in production, reducing the risks of delivering/distributing/commercialising faulty products. Larger number of tests leads to more durable materials and products.
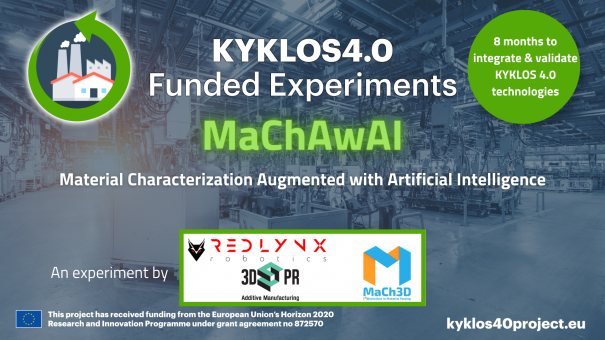