MeMOM provides the following functionalities:
- Automated scheduling and planning, including:
- rough cut capacity planning
- backward planning
- finite capacity planning
- dispatching
- Resources management
- Traceability
- Quality control
- Product Lifecycle Management
IoT & automation systems integration
MeMOM helps the manufacturing businesses in the following areas:
REDUCTION OF CORPORATE ADAPTATION TIME
Every minute of delay in decision making generates costs or decreases gains (especially in highly volatile production). We will shorten change management process by implementing near-real time insights and analysis capabilities as well as instant decision making and changes implementation.
REDUCTION IN RESOURCES USAGE
Thanks to better scheduling, monitoring execution in near-real time and earlier reaction for any irregularities, you will observe a decrease of about 1-10% in resources usage (electric energy, materials). Our scheduling algorithms can prioritise scrap reuse and electric energy consumption minimisation.
REDUCTION IN NUMBER OF DEFECTS
Thanks to specific quality control models for particular products, production tasks and steps, automatization of the QC and rework processes, IoT integration for inline quality control, we will reduce significantly number of defects that appear during the production process and amount of wasted resources, translating into significant costs reduction (5-20%).
IMPROVEMENT IN OEE / OLE
Our solution provides improvements in efficiency of resources usage thanks to built-in scheduling and dispatching algorithms, impossible to make use of manually in such short time by planners as well as visual identification of problems and improvements areas. As a result, you receive better return rates from the investments in machines and optimise employment.
RELIEF FOR PLANNERS
MeMOM keeps planning, scheduling and dispatching processes always up to date, it is adapted to the current shop floor situation. Changes in schedules are shared with all process participants in the same time. MeMOM deals with make-to-order and make-to-stock production models as well as combination of the two. Depending on the size of organisation, MeMOM can carry out everyday work of 1-10 planners.
FULL TRACEABILTY OF THE MANUFACTURING OPERATIONS
MeMOM provides performance tracking and end-to-end traceability of the products (insights into details of a single piece). This gives you view into the path the product has taken which is crucial for solving future issues (e.g. complaints, quality issues), preparing a product passport and supporting green economy (e.g. LCA/LCI calculation).
MeMOM is accessible through www.memom.solutions.
Regarding circular indicators:
CIR1 – MeMOM provides a functionality of materials tracking, including scrap. The scheduling functionality can be used with scrap re-use priority, which translates into lower use of raw materials (up to 15%).
CIR2 – In some branches, the scrap can be reused, for instance in plastic injection moulding the remaining of faulty products can be grinded and reused. By tracking the scrap in MeMOM, the usage of recyclable resources can be increased by 1-15%.
CIR3 – Thanks to better scheduling, monitoring execution in near-real time and earlier reaction for any irregularities, a decrease of about 1-10% in resources usage (electric energy, materials) is possible. Our scheduling algorithms can prioritise scrap reuse and electric energy consumption minimisation.
CIR4 – MeMOM provides a functionality of alerting if a deviation in the electric energy consumption is observed through sensors installed on machines. This most often means that a maintenance service is required and MeMOM can automatically schedule maintenance tasks for a particular machine, where the anomaly was observed. Such functionality allows to prolong a lifecycle of the machines by a few years.
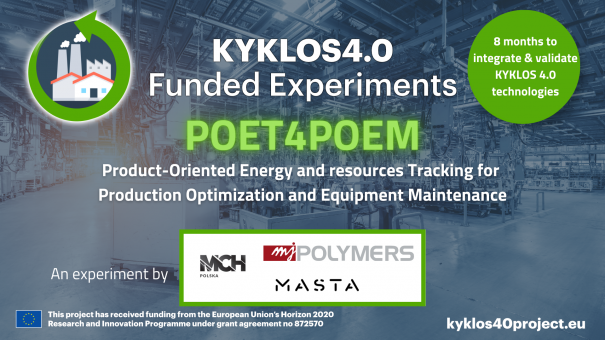