Virtfuse integrates data from curing sensors and temperature measurements, combined with RGBT camera. Through the development of AI models Virtfuse firstly, designs a model to evaluate products and assign scores to products upon finalization and secondly, it employs a model to predict the catalyst/resin ratio based on temperature for optimizing production processes and reducing waste. A user-friendly dashboard is created to gather data from cameras and sensors and visualize the entire infusion process.
Virtfuse is an innovative solution that combines data from the curing and temperature sensor and RGBT camera, utilizing AI models to achieve two primary objectives. Firstly, it designs a model for product evaluation, assigning scores for efficient quality assessment. Secondly, it employs a model to predict and optimize catalyst/resin ratios based on current temperature. The user-friendly dashboard gathers data from cameras and sensors, providing a visual representation of the entire infusion process.
VirtFuse incorporates maintenance paradigms for the oil pump and mold release agent, establishing a pipeline for efficient planning and execution of maintenance tasks. The system alerts the manager for timely interventions, ensuring optimal performance and reliability of the vacuum infusion process.
The AI analysis involves Score Function Estimation and Bayesian Optimization models. The former evaluates infusion process quality based on room temperature and catalyst/resin ratio, utilizing a Self-Attention model. Bayesian Optimization identifies optimal combinations using Gaussian processes on the input space, enhancing the quality control function.
The dashboard caters to different user roles, allowing admin users to control experiments. It features tabs for starting new experiments, providing real-time data, images, and charts for monitoring progress. Upon completion, the summary page offers infusion scores, RGB and thermal images, room temperature, and curing level graphs for download, enhancing overall monitoring and evaluation of infusion processes.
Main features of VirtFuse:
- Calculation of the optimal resin/catalysts mix ratio allowing for real-time adaptation to temperature changes.
- Visualization through a dedicated dashboard
- Assessment of each Infusion process
- Predictive maintenance enabling
Required Inputs:
- Temperature Sensors readings
- Curing Sensor reading
- RGBT camera
Regarding circular indicators:
CIR1 – Optimizing the resin mix ratio can lead to a significant increase in process efficiency and a reduction in energy consumption, material waste, and failed infusions. This is because an optimal resin mix ratio will ensure that the resin is cured properly and that the desired properties of the final product are achieved. As a result, there is less need for reprocessing, which increases energy savings and reduces waste. Additionally, an optimal resin mix ratio can help to reduce the number of failed infusions and consequently scrapped products which is the main cause of material waste. Reduced Feedstock Intensity: start: 1.125, end: 1.03
CIR4 – Using the optimal resin mix ratio ensures that the product cures properly, resulting in improved material properties and overall product quality, as evidenced by the reduced need for repairs.
CIR5 – Energy consumption reduction leads to an overall lower environmental footprint.
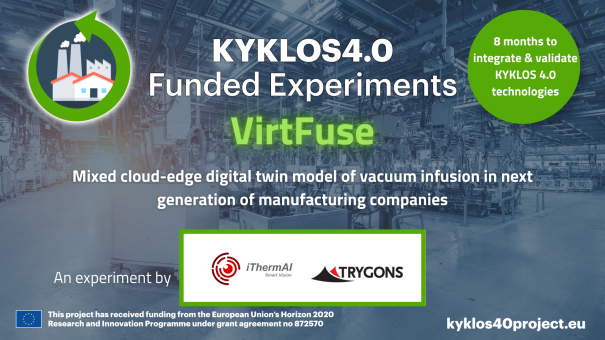